How To Implement Health And Safety At Work?
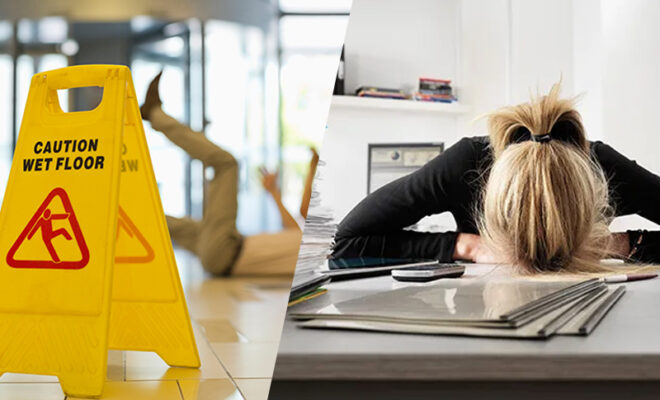
The 28th April is the World Day for Safety and Health at Work. So today we will discuss the 5 best ways to implement health and safety at work.
The obvious correlation between a safe workplace and increased output holds true. Companies benefit much from having hard working personnel.
For instance, a company’s operating costs can be lowered if its workers are efficient at what they do and produce more in the same amount of time.
Maintaining a safe workplace is good for business and the health of its employees. The health benefits of increased safety are obvious. Employees who take care of their health tend to be happier and more productive.
5 Ways To Implement Health And Safety At Work
1. Identify Workplace Hazards
You must first be aware of the health and safety concerns before you can create a safe working environment. Otherwise, dealing with them would be challenging.
Mechanical problems, hazardous chemicals, dangerous electrical equipment, and other factors might pose a risk to workplace safety.
While using machinery at work, mechanical issues can arise at any time. Working with heavy equipment is also quite dangerous and can result in accidents.
Employees must exercise extreme caution when handling chemicals. Risky chemicals can poison or burn workers. It is even fatal to breathe them in or consume them.
Additionally, using electronic equipment can be risky. Electrical equipment that is broken can electrocute workers, which is a serious issue.
Employees need to be informed of the many types of equipment and hazards at work. They are able to avoid these risks and terrible circumstances as a result.
Establishing possible danger areas should therefore be a primary goal, and working with your staff to reduce such hazards will be effective. Employers should also instruct staff members on how to use machinery and equipment properly.
2. Introduce workplace safety initiatives
Getting all employees to make a commitment to workplace safety is the first step in creating a safety program.
Including occupational health and safety in the organization’s mission statement is one method to achieve this. Every employee should be responsible for following the safety regulations.
Every workplace accident should be looked into by the employer. They ought to motivate staff to adhere to all safety guidelines.
The risks of not adhering to them should also be expressly mentioned in writing. This lessens the likelihood of errors.
3. Educate employees on proper safety procedures
Every company’s safety program includes training as a crucial component to safeguard personnel from mishaps.
New hires are more likely to be involved in workplace accidents, according to research. This greater risk is brought on by an ignorance of workplace dangers and safe working practices.
To lower workplace accidents, employers should give workers the appropriate training. All machinery and equipment should be operated by staff members safely and effectively.
For instance, workers need to be well trained in the use of heavy equipment. Such equipment should only be operated by those who have been trained or qualified. This is why it’s crucial to give staff expert-led safety training.
4. Make use of protective safety gear
It’s crucial to utilize protective gear to reduce exposure to risks that lead to work-related injuries. Failure to do so may result in harm or even death.
Employees could be required to work with hazardous materials like chemicals, machinery, electronics, and other things. Employers are required to supply personal protection equipment (P.P.E.) to certain workers.
P.P.E. should be constructed, fitted, and designed safely. Gloves, safety goggles, protective gear, earplugs, hard helmets, and other items are examples of P.P.E.
5. Identify Dangerous Working Conditions
Any safety danger or job risk must be reported by employees to management. Legally, employers must make sure that their workers have a safe place to work. They must eliminate workplace safety risks and advance workplace security.